For ESI undergraduate engineer Lars Sobieski, space hardware is both tech and art
Lars Sobieski, undergraduate mechanical engineer at the Earth and Space Institute, spends his day developing hardware and testing for future climate satellites. At ESI, he designs and fabricates some of the ground support equipment (GSE) that will help calibrate future climate instruments, particularly the two-dimensional focal plane arrays (FPA). The FPA is the surface of a detector that collects light across millions of pixels and converts it into an image. ESI is developing FPAs for upcoming satellite instruments that are sensitive to ultraviolet (UV), visible (VIS), and shortwave infrared (SWIR) wavelengths. These are critical spectral ranges for studying Earth’s clouds, aerosols, land, ocean, and atmosphere.
A major type of testing that satellites and their detectors undergo before launch is thermal vacuum (TVAC) testing. In the lab, Mr. Sobieski and ESI faculty are preparing an industrial TVAC chamber, which can submit our space hardware to orbit temperatures (-20C to +20C) and space-like pressures (10-7 millibars and lower). This TVAC chamber was part of a major state grant to ESI, led by Maryland Senators Ben Cardin and Chris Van Hollen, to boost UMBC’s capacity to support new space and satellite projects.
Mr. Sobieski is currently helping to optimize the TVAC chamber for related testing. However, he explains, “Because the TVAC chamber will not be ready for use for some of the FPA tests, I was given the task of designing and building an enclosure that can fit the GSE needed for the UV/VIS FPA test. This enclosure will be purged with dry air to ensure that no condensation will form on the electronics as they are chilled to below the dewpoint. It must also isolate the FPA from electrostatic discharge and provide through-wall access points for power, data, pneumatics, and a liquid cooling loop.” This will be used to verify the operation of the FPA prior to testing it under day-night temperature swings or the low pressures of the orbit environment.
Photo: The full assembly of the UV/VIS FPA (center gray part) and associated electronics in a metal enclosure for electronics testing. Photo Credit: L. Sobieski/ESI.
Since March 2025, he took on a completely different project for ESI in parallel – developing a full-scale 3D-printed model of the HARP CubeSat, ESI’s first foray into small satellite technology for studying Earth’s climate. According to Mr. Sobieski, “The process involved using the existing CAD assembly of the CubeSat to create a new, simplified model from scratch to reduce the part count. While the actual CubeSat had a few thousand parts, the 3D-printable model has only nineteen.” After a few rounds of test prints, gluing, body-filling, sanding, and priming, Mr. Sobieski enlisted the help of his fiancée to do the detail brush painting. For the end result, the 3D model of the HARP CubeSat looks remarkably similar to what actually flew in space from 2020-2022.
Photos: Process composite of the development of the HARP CubeSat 3D model. The monobloc model derived from the original satellite CAD file (left), components were primed (center left), painted to match the satellite (center right), and the final model (right). Photo Credit: L. Sobieski/ESI.
Posted: July 22, 2025, 2:37 PM
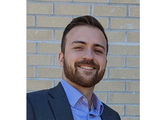